Gv Automation Engineering Inc
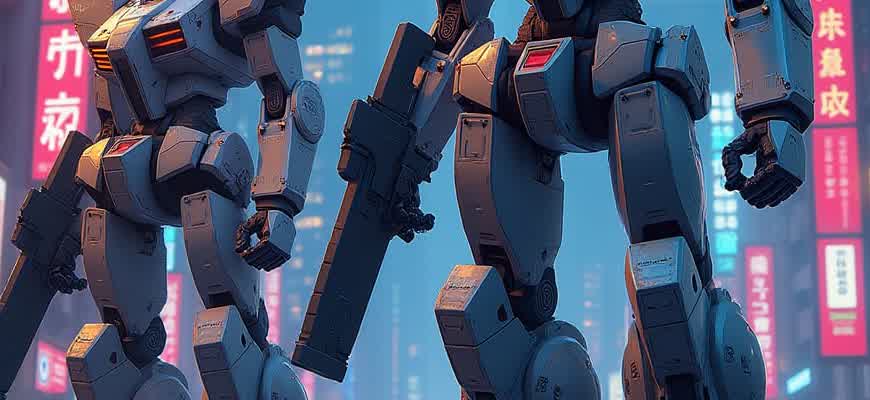
Gv Automation & Engineering Inc is a leading provider of advanced automation and engineering solutions, specializing in delivering customized systems that enhance efficiency across various industries. With a focus on innovation and high-quality standards, the company has built a reputation for reliability and precision in its project execution.
The company's core services are organized into several key areas:
- Automation Systems Design and Integration
- Industrial Control Solutions
- Engineering Consulting and Project Management
- Maintenance and Support Services
"Delivering cutting-edge automation technology tailored to meet the unique needs of every client."
In terms of operational approach, Gv Automation & Engineering Inc prioritizes the following methodologies:
- Comprehensive analysis and planning before project initiation.
- Implementation of state-of-the-art automation technologies.
- Continuous monitoring and support post-implementation.
Below is a summary of the company's key service offerings:
Service | Description |
---|---|
System Integration | Seamless integration of automation systems into existing infrastructures. |
Custom Engineering Solutions | Design and development of bespoke engineering solutions tailored to specific client needs. |
Consulting | Expert advice on system optimization and technological upgrades. |
Streamlining Operations with Tailored Automation Solutions
In today’s fast-paced industrial landscape, efficiency is paramount. Custom automation systems are essential for businesses aiming to streamline their operations and optimize productivity. By tailoring solutions to specific needs, companies can improve operational workflows, reduce human error, and ensure seamless integration across various processes.
GV Automation & Engineering Inc. specializes in delivering precision-engineered automation solutions designed to meet the unique demands of each client. These systems provide a significant advantage in terms of scalability, adaptability, and performance, ensuring businesses can grow without the constraints of outdated technology.
Key Benefits of Custom Automation Solutions
- Increased Efficiency: Automated processes eliminate bottlenecks, speeding up production cycles and reducing downtime.
- Improved Accuracy: Precision systems reduce the risk of human error, ensuring consistency in output quality.
- Cost Savings: Automation helps reduce labor costs and waste, directly impacting the bottom line.
- Scalability: Tailored solutions grow with your business, allowing for easy adaptation to changing needs.
Automation Integration Process
- Assessment: Conduct a thorough analysis of the existing workflow to identify areas for improvement.
- Design: Create a custom automation plan based on client needs and industry requirements.
- Implementation: Integrate the automation system with minimal disruption to ongoing operations.
- Optimization: Continuously monitor system performance and make necessary adjustments for maximum efficiency.
“Tailored automation is not just about replacing manual labor; it's about enhancing overall system performance and positioning your business for sustainable growth.” – GV Automation & Engineering Inc.
System Performance Comparison
Metric | Before Automation | After Automation |
---|---|---|
Production Speed | 50 units/hour | 120 units/hour |
Downtime | 15% | 2% |
Error Rate | 8% | 0.5% |
How GV Engineering Minimizes Downtime in Production Systems
GV Engineering provides innovative solutions that help manufacturers reduce production downtime. Through advanced automation systems and engineering strategies, they optimize manufacturing processes and ensure continuous operation. By focusing on real-time diagnostics, predictive maintenance, and efficient system integration, they help businesses avoid costly interruptions.
One of the primary ways GV Engineering mitigates downtime is by enhancing machine reliability and providing immediate responses to system malfunctions. Their approach includes integrating cutting-edge sensors and AI-driven analytics to predict failures before they occur. This preemptive strategy ensures that manufacturers can address issues proactively, rather than reactively, preventing significant production losses.
Key Strategies Employed by GV Engineering
- Predictive Maintenance: By using data analytics and machine learning, GV Engineering can forecast potential issues, allowing businesses to schedule maintenance activities during non-peak times.
- Automated Diagnostics: Advanced diagnostics tools identify problems instantly, providing technicians with clear insights into the root cause of an issue.
- Real-Time Monitoring: Continuous monitoring systems allow for immediate identification of abnormal behaviors in equipment, reducing the time it takes to pinpoint and fix issues.
Impact of GV Engineering's Approach
Strategy | Benefit |
---|---|
Predictive Maintenance | Minimizes unplanned downtime and extends the life of equipment. |
Automated Diagnostics | Reduces diagnostic time and accelerates issue resolution. |
Real-Time Monitoring | Improves response times and reduces system failures. |
"By implementing GV Engineering's automated solutions, we have significantly reduced our production downtime and improved overall efficiency," says a long-time client in the automotive sector.
Integrating AI and Machine Learning into Automation Systems
As the industrial landscape evolves, the integration of artificial intelligence (AI) and machine learning (ML) into automation systems is transforming operational efficiency. The traditional methods of automation, while effective, often lack the adaptive capabilities required for highly dynamic environments. By leveraging AI and ML, automation systems can achieve predictive capabilities, optimize workflows, and make real-time decisions that improve both production and maintenance outcomes.
AI and ML are becoming integral parts of industrial automation, enabling systems to learn from data, adapt to new conditions, and improve performance over time. This shift towards smart automation allows companies to not only reduce human intervention but also enhance precision and scalability. The combination of these technologies in automation systems offers significant opportunities for increased productivity and cost savings.
Key Advantages of AI and ML Integration
- Predictive Maintenance: AI and ML algorithms analyze sensor data to predict failures before they occur, reducing unplanned downtime and maintenance costs.
- Optimized Operations: Machine learning models process historical data to suggest process improvements and adjust operations in real-time for maximum efficiency.
- Quality Control: AI can detect anomalies in production lines, ensuring products meet quality standards without human intervention.
- Process Automation: Machine learning algorithms can automate decision-making processes based on past outcomes, leading to faster and more accurate operations.
Challenges in Integration
Despite the numerous benefits, integrating AI and ML into automation systems presents challenges such as data quality issues, the need for specialized skills, and the initial investment costs.
- Data Quality: Accurate and clean data is crucial for training ML models. Inconsistent or incomplete data can hinder the performance of AI-based automation systems.
- Skills Gap: Implementing AI and ML requires skilled professionals, making it difficult for some organizations to adopt these technologies without proper training.
- Initial Investment: While AI-driven automation can lead to long-term savings, the upfront investment required for infrastructure and technology can be significant.
Impact on Future Automation Trends
Trend | Impact |
---|---|
Real-time Decision Making | AI and ML enable systems to make immediate decisions based on real-time data, improving responsiveness and flexibility. |
Self-Optimizing Systems | Automation systems can continuously improve their own performance through self-learning algorithms, reducing the need for manual interventions. |
Advanced Robotics | AI-powered robots will become more adept at handling complex tasks in dynamic environments, pushing the boundaries of what automation can achieve. |
Customized Electrical Engineering for Enhanced Performance
At Gv Automation & Engineering Inc., our approach to electrical engineering is designed to optimize the performance of your systems. We focus on tailored solutions that address the specific needs of each project, ensuring that the final output exceeds expectations. By integrating advanced technology with precise engineering practices, we deliver results that maximize operational efficiency and reliability.
Our engineering team works closely with clients to develop systems that are not only efficient but also adaptable to future needs. Through detailed assessments and specialized designs, we create electrical solutions that are as dynamic as the industries they serve. The result is a streamlined process that boosts productivity while minimizing downtime and operational costs.
Key Benefits of Tailored Electrical Engineering
- Increased Efficiency: Custom-designed electrical systems maximize energy usage and operational output.
- Scalability: Flexible solutions that can evolve with business growth and changing demands.
- Reduced Downtime: Robust systems that require minimal maintenance and are engineered for long-term reliability.
Our Approach to Tailored Electrical Systems
- Initial Consultation: Understanding client needs and operational goals.
- Custom Design: Developing a detailed plan based on the unique requirements of each project.
- Implementation: Installing and testing systems to ensure peak performance from day one.
- Continuous Support: Offering ongoing service and optimization for sustained output.
"We believe in creating systems that not only meet the demands of today but are ready for the challenges of tomorrow." – Gv Automation & Engineering Inc.
Examples of Our Tailored Electrical Engineering Solutions
Industry | Solution | Outcome |
---|---|---|
Manufacturing | Automated production lines with custom power systems | Reduced energy consumption, improved throughput |
Healthcare | Specialized electrical setups for medical equipment | Increased reliability, minimized system failures |
Construction | Site-specific power distribution networks | Enhanced worker safety, optimized energy use |
Enhancing Safety Protocols Through Automation in High-Risk Environments
In industries involving hazardous materials, heavy machinery, or high-velocity systems, maintaining strict safety standards is crucial. Automation has become a key player in improving safety protocols, particularly where human involvement can increase the potential for accidents. By integrating automated systems into these environments, companies can reduce human error, ensure consistent monitoring, and improve response times during emergencies. Automation in high-risk sectors includes the use of robotic systems, sensors, and AI-driven processes that monitor safety parameters in real time.
One of the most significant benefits of automation is its ability to continuously monitor and control hazardous processes without human intervention. Automated systems are capable of taking preventive actions in case of an anomaly or abnormal condition, offering a level of precision and reliability that humans alone cannot match. Furthermore, automation helps in reducing human exposure to dangerous tasks, which is essential for minimizing injury risks. These systems are designed to quickly identify issues, allowing for rapid response and mitigation of potential threats.
Key Benefits of Automation in Safety Protocols
- Real-Time Monitoring: Automated systems can constantly monitor critical parameters like pressure, temperature, and chemical composition, providing immediate alerts if a threshold is crossed.
- Reduced Human Error: Human mistakes are minimized in environments where automated systems perform high-stakes tasks, reducing the risk of accidents caused by lapses in judgment or fatigue.
- Faster Emergency Response: Automation allows for rapid intervention during safety breaches, such as shutting down machinery or activating emergency containment measures without delay.
Automated Safety Features in High-Risk Sectors
- Industrial Robotics: Robots can replace human workers in tasks that expose them to dangerous conditions, such as handling toxic substances or working in extreme temperatures.
- Predictive Maintenance: AI-powered predictive systems can analyze equipment wear and tear, scheduling maintenance before failures occur, which prevents catastrophic breakdowns.
- Advanced Sensors: Integrated sensors are capable of detecting hazardous situations such as gas leaks or electrical malfunctions and can automatically trigger safety protocols.
Impact of Automation on Safety Outcomes
"Automation not only improves safety by preventing accidents but also enhances operational efficiency, creating a more secure environment for employees and stakeholders."
Technology | Benefit |
---|---|
Robotics | Reduces exposure to hazardous environments |
Predictive Maintenance | Prevents unexpected failures and downtime |
Automated Sensors | Enables immediate response to safety breaches |
Troubleshooting Automation Failures in Production Lines
Production lines are a cornerstone of modern manufacturing, and automation systems play a vital role in ensuring efficient, high-quality output. However, like any complex system, automated production lines are susceptible to a variety of failures. Diagnosing these issues promptly is crucial to minimizing downtime and maintaining productivity. The following section outlines common automation failures and provides targeted troubleshooting steps to resolve these issues effectively.
Whether it's a malfunctioning sensor, a PLC program bug, or a mechanical breakdown, each issue demands a systematic approach. Identifying the root cause of the failure is essential for preventing recurrence and improving overall system reliability. The following guide covers several common automation failures and how to troubleshoot them with minimal disruption.
Common Automation Failures and Troubleshooting Steps
- Sensor Failures: Sensors play a critical role in data collection and feedback for automation systems. When a sensor malfunctions, it can result in incorrect readings, leading to production issues.
- PLC Errors: Programmable Logic Controllers (PLCs) are the brains behind most automation systems. Errors in PLC programming or hardware malfunctions can disrupt the entire production process.
- Mechanical Failures: Mechanical components such as motors, conveyors, or actuators often face wear and tear. These failures can be difficult to spot until they cause a complete breakdown.
Steps for Troubleshooting
- Check System Logs: Start by reviewing system logs for any error codes or irregularities. This can quickly highlight where the problem lies.
- Verify Sensor Calibration: Ensure that all sensors are properly calibrated. Misalignment or dirt on the sensor can cause erroneous readings.
- Inspect PLC Program: Run diagnostic tests on the PLC program to ensure that all commands are being processed correctly. Debugging the program can help identify logic errors.
- Perform Visual Inspections: A visual inspection of mechanical components can often reveal obvious signs of wear, loose connections, or misalignments.
For a more systematic approach, document all troubleshooting steps and outcomes. This log can serve as a valuable reference for future maintenance and help in recognizing recurring issues.
Key Troubleshooting Checklist
Issue | Possible Causes | Actions |
---|---|---|
Sensor Failure | Dirty sensor, misalignment, faulty wiring | Clean sensor, check wiring, recalibrate sensor |
PLC Error | Program bug, hardware malfunction, communication failure | Check code, reset PLC, test inputs and outputs |
Mechanical Breakdown | Wear and tear, lack of lubrication, misalignment | Inspect components, lubricate moving parts, replace damaged parts |
Designing Scalable Systems for Growing Industrial Demands
As industries evolve and face increasing operational requirements, the ability to scale systems efficiently is paramount. Designing adaptable solutions for industrial environments necessitates the integration of robust technologies that support both current and future demands. To meet this challenge, it is essential to focus on flexibility, automation, and precision. These systems must be designed with growth in mind, ensuring that they can handle increasing workloads without compromising performance.
The foundation of a scalable system lies in its architecture. Engineers must leverage modular designs that allow for easy upgrades and expansions. This approach ensures that organizations can adapt to new market conditions and technological advancements without overhauling entire systems. The right balance between scalability and performance is achieved by adopting a forward-thinking design strategy.
Key Considerations in System Design
- Flexibility: Systems should be designed to adapt to different operational needs and environments.
- Automation: Automated processes help reduce human intervention, increasing efficiency and minimizing errors.
- Modularity: Modular designs allow for easy upgrades and expansion, making future scaling more efficient.
- Data Integration: Seamless data flow between different components is critical for optimized system performance.
Steps for Creating Scalable Industrial Systems
- Assess Current Needs: Understand the current operational demands and identify potential bottlenecks.
- Future-Proof Design: Incorporate design principles that allow for future growth without significant system overhaul.
- Implement Automation: Introduce automated solutions that scale alongside the growing demands of the industry.
- Monitor and Optimize: Continuously assess system performance and optimize for efficiency as production scales.
"The key to scalability in industrial systems lies in a thoughtful balance between adaptability, automation, and future-proof design." – Expert Opinion
Sample System Scalability Breakdown
Component | Initial Design | Scalability Consideration |
---|---|---|
Control System | Basic automated control with minimal capacity | Expandable control architecture for increased load |
Power Supply | Standard power distribution | Modular power units for additional energy demand |
Monitoring System | Single location monitoring | Distributed network for real-time data collection across multiple sites |
Cost Analysis of Implementing Automation Solutions in Different Industries
Automation solutions play a crucial role in enhancing productivity, efficiency, and cost-effectiveness across various industries. However, the financial impact of integrating automation varies depending on the sector, the scale of implementation, and the complexity of the systems involved. Companies must evaluate both short-term costs and long-term savings when considering the introduction of automation technologies. This evaluation ensures that the investments align with their business objectives and yield positive returns.
In sectors like manufacturing, automation can significantly reduce labor costs, improve product quality, and minimize downtime. However, the initial investment in automation systems, training, and integration can be high. Conversely, industries such as healthcare and logistics experience a more gradual impact, where automation optimizes processes like patient care or inventory management, offering substantial operational efficiencies over time.
Key Factors Influencing Automation Costs
- Initial Investment: Automation systems require substantial upfront costs for equipment, software, and infrastructure.
- Maintenance and Support: Ongoing maintenance and system updates can add to operational expenses.
- Training: Employees need to be trained to work with new automated systems, which can incur additional costs.
- Scale of Implementation: Larger companies or those with complex operations may face higher integration costs due to the need for customized solutions.
Cost Breakdown for Different Industries
Industry | Initial Investment | Long-Term Savings |
---|---|---|
Manufacturing | High | Significant reduction in labor costs and production errors |
Healthcare | Moderate | Improved efficiency and reduced human error in patient care |
Logistics | Moderate | Faster delivery times and reduced inventory holding costs |
"The ROI of automation is not always immediate, but over time, it can lead to exponential cost savings and efficiency improvements."
Considerations for Successful Implementation
- Clear Objectives: Companies should define their goals for automation, such as improving production speed or enhancing accuracy.
- ROI Analysis: A detailed return-on-investment analysis helps identify which areas will benefit the most from automation.
- Scalability: Businesses must choose automation systems that can scale as the company grows or adapts to market changes.